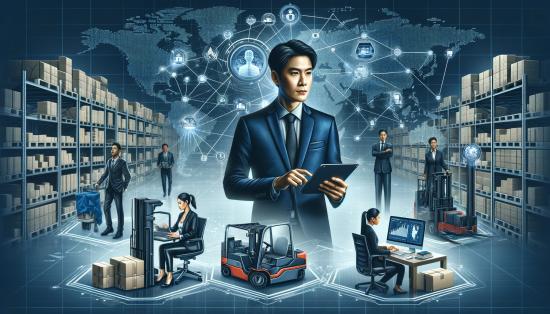
Mastering Inventory Management: Key Strategies for an Optimized Supply Chain
Learn the art of effective inventory management to optimize your supply chain. Reduce costs and improve customer satisfaction with these strategies.
Introduction to the significance of inventory management in supply chain optimization. Effective inventory management plays a critical role in ensuring a smooth and efficient supply chain. By maintaining optimal inventory levels, organizations can minimize stockouts, reduce carrying costs, and enhance customer satisfaction. It also enables businesses to make informed decisions about purchasing, production, and distribution, ultimately leading to cost savings and improved operational performance.
Understanding the basics of inventory management is crucial for the seamless flow of goods and materials in the supply chain. Inventory management directly impacts logistics by ensuring the right products are available at the right time and in the right quantities. Efficient inventory management helps in reducing stockouts, overstocking, and carrying costs, ultimately streamlining the logistics process. By monitoring inventory levels and demand patterns, companies can make informed decisions to optimize transportation, storage, and distribution activities. Additionally, accurate inventory management contributes to improved customer satisfaction and retention as it enables timely order fulfillment and delivery.
The role of technology in streamlining inventory tracking and management processes is essential for the modern supply chain. With the use of advanced software and hardware solutions, businesses can automate and centralize their inventory control, resulting in increased accuracy and efficiency. RFID technology, barcode scanning, and inventory management software enable real-time visibility of stock levels, reducing the risk of stockouts and overstocking. Additionally, technology allows for better demand forecasting and analysis, leading to improved inventory accuracy and optimized replenishment processes. By leveraging technology, businesses can streamline their inventory tracking and management, ultimately driving cost savings and operational performance.
Implementing just-in-time (JIT) inventory is a strategic approach to minimize waste and enhance efficiency in supply chain operations. By aligning inventory levels closely with actual demand, companies can reduce excess inventory storage costs, minimize the risk of stockouts, and improve overall operational efficiency. JIT inventory management requires a seamless coordination between production schedules, supplier deliveries, and customer demand forecasts to ensure the right amount of inventory is available at the right time. This lean approach to inventory management enables companies to optimize working capital, reduce carrying costs, and enhance responsiveness to market fluctuations, ultimately driving cost savings and competitive advantage.
Adopting a demand forecasting approach offers several key advantages for improving inventory accuracy. By utilizing historical sales data and market trends, companies can predict future demand with greater accuracy, allowing for more precise inventory planning. This enables businesses to minimize overstocking or stockouts, reduce carrying costs, and optimize working capital. Additionally, demand forecasting enhances supply chain efficiency by aligning inventory levels with actual demand, resulting in improved customer service, reduced lead times, and lower production costs. Furthermore, accurate demand forecasting provides valuable insights for strategic decision-making, such as identifying potential market opportunities, optimizing pricing strategies, and improving overall business performance.
Strategies for warehouse optimization are crucial for effective inventory management and overall supply chain efficiency. One key strategy is to reorganize the layout of the warehouse to maximize space utilization and minimize travel time for picking and packing. This can involve implementing a systematic approach to the storage of inventory, such as using ABC analysis to prioritize high-demand items. Additionally, adopting advanced technologies like RFID and barcode systems can streamline inventory tracking and help in maintaining accurate stock levels. Implementing cross-docking and zone picking methods can also reduce handling and storage costs, while improving order fulfillment speed. Furthermore, establishing clear inventory control policies and regular cycle counting processes are essential for maintaining accuracy and preventing stockouts or overstock situations.
Maintaining appropriate inventory levels is crucial for the smooth operation of supply chain management. One of the key factors in achieving this goal is supplier relationship management. Cultivating strong relationships with suppliers can provide several benefits, such as improved lead times, better pricing, and greater flexibility in managing inventory levels. By establishing clear communication channels and working closely with suppliers, companies can gain better insights into market trends, demand fluctuations, and potential disruptions, allowing for more accurate inventory planning. Additionally, strong supplier relationships can lead to collaborative problem-solving and continuous improvement initiatives, ensuring the reliable flow of materials and products to sustain optimal inventory levels.
Leveraging data analytics to make informed decisions about inventory management is crucial for optimizing supply chain operations. By harnessing the power of data, businesses can gain valuable insights into demand patterns, consumption trends, and seasonal fluctuations, enabling them to align inventory levels with actual market needs. Data analytics provides the visibility and predictive capabilities necessary to make accurate forecasts, minimize stockouts, reduce carrying costs, and improve overall efficiency. With the right data-driven approach, companies can make proactive decisions to enhance inventory accuracy, streamline replenishment processes, and ultimately drive cost savings while maintaining optimal inventory levels.
In conclusion, continuous improvement in inventory management is essential for achieving supply chain success. By constantly optimizing and refining inventory processes, companies can reduce carrying costs, minimize waste, and enhance operational efficiency. Through the strategic implementation of just-in-time inventory, demand forecasting, warehouse optimization, and leveraging data analytics, organizations can maintain optimal inventory levels and align them with market demand. This approach not only drives cost savings but also ensures that the right products are available at the right time, ultimately improving customer satisfaction and competitiveness in the market.
Related posts
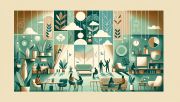
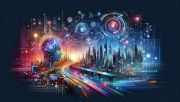